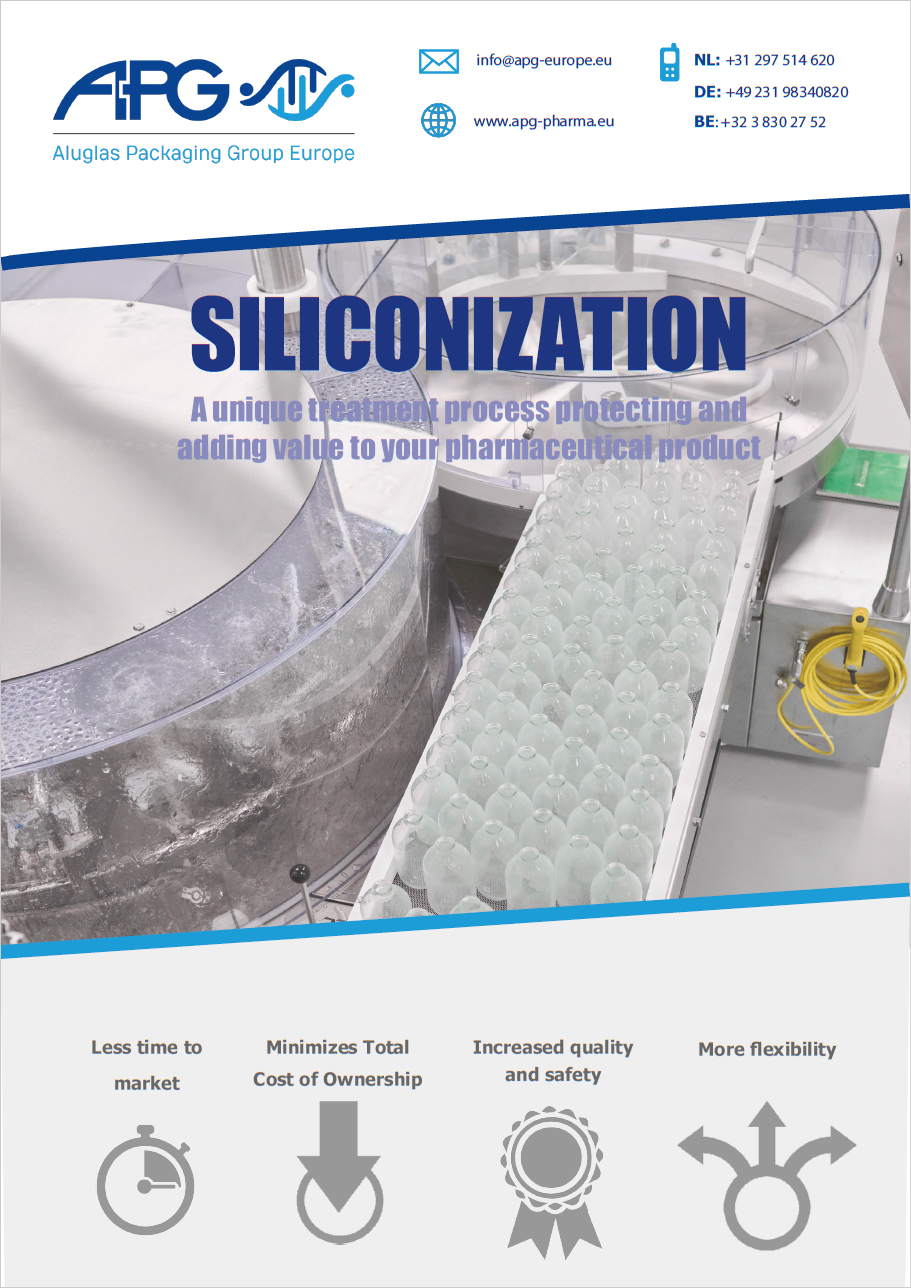
Siliconization
Siliconization of Vials and Bottles
Advanced Protection for Pharmaceutical Products: Siliconization is a specialized process that applies a valuable, protective layer to the interior of glass vials and bottles. This process provides a robust solution for sensitive, aggressive, and viscous pharmaceutical products, minimizing interactions between the product and the packaging. As a result, both the quality of the drug and patient safety are ensured. Additionally, siliconization contributes to a more efficient supply chain and minimizes the Total Cost of Ownership.
The Siliconization Process and Its Benefits
- Barrier Effect: Glass is not inert and can release volatile substances (leachables), such as metal ions, which react with the drug. This can lead to oxidation, fragmentation, and aggregation of proteins, which can have harmful consequences for the product's stability. Siliconization creates a robust hydrophobic coating inside the vial, minimizing these interactions and forming a barrier against ion exchange. Furthermore, this coating provides additional chemical resistance to alkaline solutions (pH > 7), preventing the migration of aluminum from the glass.
- Hydrophobic Properties: Siliconization of vials prevents viscous liquids from sticking to the inside of the glass, allowing for higher restitution of the content. This is crucial for administering the correct dosage of the drug. The hydrophobic nature of the silicone layer also ensures optimal transparency of the bottle, which is important for the visual inspection of the content.
- Reconstitution Factor: After siliconization, the reconstitution of powdered drugs in Water For Injection (WFI) or other solvents is significantly faster and easier, contributing to more efficient preparation of the drug for administration.
Step-by-Step Siliconization Process
- Loading: The vials are received in shrink-wrapped packaging, inspected, and then placed on the conveyor belt.
- Pre-washing: The vials are pre-washed with qualified water to remove impurities.
- Washing: A thorough cleaning with qualified water ensures the vials are completely clean before the siliconization process begins.
- Drying: Both internal and external drying occurs to remove excess moisture before the silicone solution is applied.
- Siliconization: A polydimethylsiloxane emulsion is sprayed inside the vials. This emulsion meets all pharmacopeia requirements and is carefully applied for an even coating.
- Annealing: The silicone film is then fixed to the glass through an annealing lehr, permanently securing the coating.
- Post-heat Treatment Quality Control: After annealing, the vials are thoroughly inspected to ensure that the coating has been correctly applied.
- Packaging: The silicone-coated vials are automatically packed in shrink-wrapped packages, ready for further processing or shipping.
- Palletizing: The packed vials are stacked on pallets and prepared for transport to the customer.
Quality Control
At APG Europe, the quality of siliconized vials is meticulously monitored at every stage of the production process. Quality control is carried out through systematic sampling and various tests to evaluate the durability and uniformity of the coating:
- Type III Glass: After a visual inspection of the glass surface, a test is performed at room temperature. The vial is evenly moistened with a synthetic solution of kaolin and glycerine, and the speed and uniformity of the solution’s retraction are measured.
- Type I and II Glass: An accelerated aging test is performed by partially filling the vials with a synthetic solution of citric acid and soda. The vials are then heated in an autoclave at 121°C for 30 minutes. After cooling, the quality of the solution’s retraction is assessed.
APG Europe’s siliconization unit meets the highest standards for quality control and operates within a class 100,000 (ISO 8) cleanroom environment. Since 2007, the facility has been ISO 15378 certified, underscoring its commitment to quality and customer satisfaction.
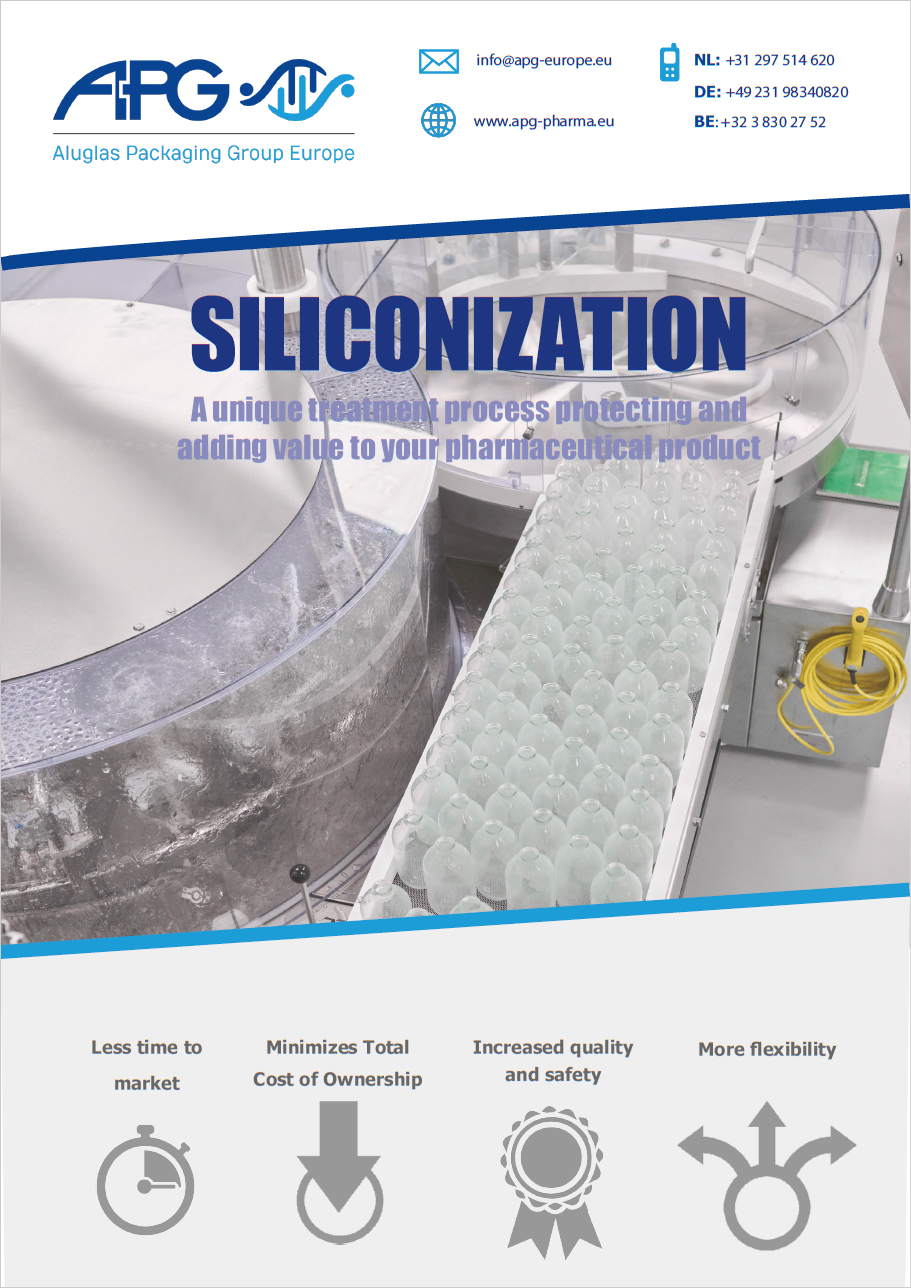
Why Choose APG Europe?
APG Europe offers more than just siliconization; we are your total packaging partner for pharmaceutical, medical, cosmetic, and food products. Through our advanced technologies, logistical solutions, and QA/QC support, we strive to provide your products with the highest level of quality and safety. Together with you, we develop the best solutions to ensure your success.